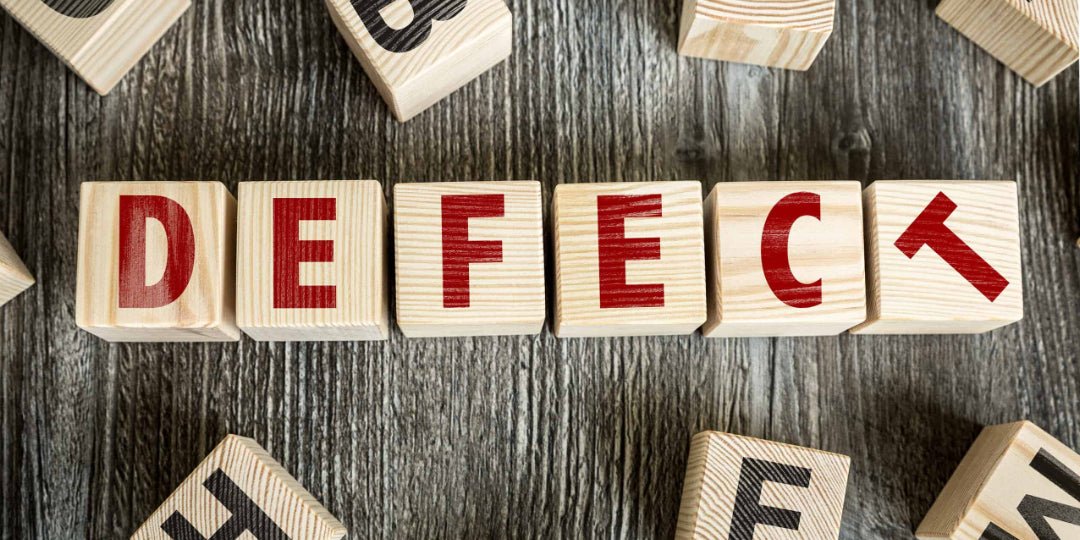
Defeat Defects: Strategies to Slash Waste and Boost Quality in Manufacturing
In our ongoing series exploring the eight wastes in lean manufacturing, we now turn our attention to a critical yet often overlooked aspect: defects. Defects represent one of the most significant forms of waste, directly impacting quality, customer satisfaction, and operational efficiency. In this fourth installment, we delve into the root causes of defects, their detrimental effects on the production process, and practical strategies to minimize and eliminate them. Join us as we uncover how addressing defects can lead to more robust and reliable manufacturing practices, driving continuous improvement and excellence in your operations.
“What are defects?”
In the context of lean manufacturing, defects refer to any product or component that fails to meet quality standards or customer specifications. This includes errors, flaws, or inconsistencies that require rework, repair, or replacement, ultimately leading to wasted resources, increased costs, and reduced customer satisfaction.
Defects aren’t only the errors that occur in our processes but can be sitting within our inventory. It’s important to note that as we are progressing through the 8 wastes, they flow into one another as a sort of “story”. We overproduced and had to transport our excess inventory to our facility, and now, within our inventory, there can be defects that we don’t even know about until we get to them.
“What causes defects?”
Here are just a few examples:
- Inadequate Training: Employees lacking proper training or understanding of the processes can make mistakes that result in defects. This underscores the need for comprehensive training programs and ongoing skill development.
- Poor Process Design: Inefficient or poorly designed processes can lead to inconsistencies and errors. This highlights the importance of process optimization and standardization to ensure consistent quality.
- Equipment Malfunctions: Outdated or poorly maintained equipment can cause production errors, leading to defective products. Regular maintenance and timely upgrades are essential to prevent such issues.
- Lack of Standard Operating Procedures (SOPs): Without clear and standardized procedures, variations in how tasks are performed can lead to defects. Implementing and adhering to SOPs can help maintain consistency and quality.
- Inconsistent Material Quality: Variations in the quality of raw materials or components can cause defects in the final product. Establishing strong relationships with reliable suppliers and conducting regular quality checks can mitigate this risk.
“We just need to train our employees better, then we won’t have as many defects.”
In lean manufacturing, the focus is on improving processes rather than blaming workers when defects occur. This perspective is rooted in the belief that well-designed processes should inherently prevent errors and ensure consistent quality.
In essence, lean manufacturing views defects as indicators that the process needs improvement. This approach not only leads to better quality and efficiency but also fosters a positive work environment where employees are supported and valued.
According to a report by the American Society for Quality (ASQ), approximately 36% of organizations cite defects and rework as significant challenges impacting their quality and efficiency (Source: ASQ, "Global State of Quality 2 Research: Discoveries 2019").
"Quality is free. It's not a gift, but it's free. The 'unquality' things are what cost money." — Philip B. Crosby, "Quality Is Free: The Art of Making Quality Certain" (1979).
“So, how can I reduce defects in my work?”
Five tools and changes that can help reduce defects are:
- Implementing Quality Control Checks:
Regular quality control checks throughout the production process can identify defects early, preventing defective products from progressing through the manufacturing line. This can include inspections at critical stages and final product evaluations to ensure compliance with quality standards.
- Implementing Failure Mode and Effects Analysis (FMEA):
FMEA is a systematic approach used to identify and prioritize potential failure modes in a process, product, or system. By analyzing potential failure modes and their effects on product quality, safety, and performance, manufacturers can proactively mitigate risks and design robust preventive measures. This proactive approach helps to reduce defects by addressing potential failure points before they impact production or customer satisfaction.
- Training and Skill Development:
Providing comprehensive training for employees ensures they understand the correct procedures and techniques required to produce high-quality products. Continuous skill development programs keep workers updated on best practices and new technologies, reducing the likelihood of human error.
- Adopting Poka-Yoke (Mistake-Proofing):
Poka-yoke devices are designed to prevent errors by making it difficult or impossible to perform a task incorrectly. These can include jigs, fixtures, and automated systems that guide workers or machines through the correct steps, ensuring consistent and error-free production.
- Improving Process Design and Standardization:
Streamlining and standardizing processes can reduce variability and eliminate opportunities for defects to occur. This includes creating detailed standard operating procedures (SOPs) and ensuring that all employees follow them consistently, leading to more uniform and higher-quality outputs.
Real World Example:
GE Aviation utilized several lean tools, including Statistical Process Control (SPC) and Failure Mode and Effects Analysis (FMEA), as part of their quality improvement initiatives. SPC was used to monitor critical process parameters and detect deviations early, while FMEA helped identify potential failure modes and prioritize preventive actions.
As a result of these efforts, GE Aviation reported significant improvements in defect reduction and overall quality performance. For example, in their jet engine manufacturing processes, they achieved a reduction in defect rates by more than 50% over a period of several years. This improvement not only enhanced product reliability and safety but also contributed to cost savings through reduced rework and warranty claims.
Embracing strategies to reduce defects isn't just about improving product quality—it's about safeguarding your business's reputation and profitability. By implementing the proven techniques discussed, you can minimize waste, boost efficiency, and deliver products that consistently exceed customer expectations. Don't wait to take action. Start transforming your manufacturing processes today to secure a competitive edge in the market.
For more insightful articles on enhancing operational efficiency and reducing waste in manufacturing, visit our website blog at https://magnaliteltd.com/blogs/news and explore how continuous improvement strategies can drive lasting success for your business.