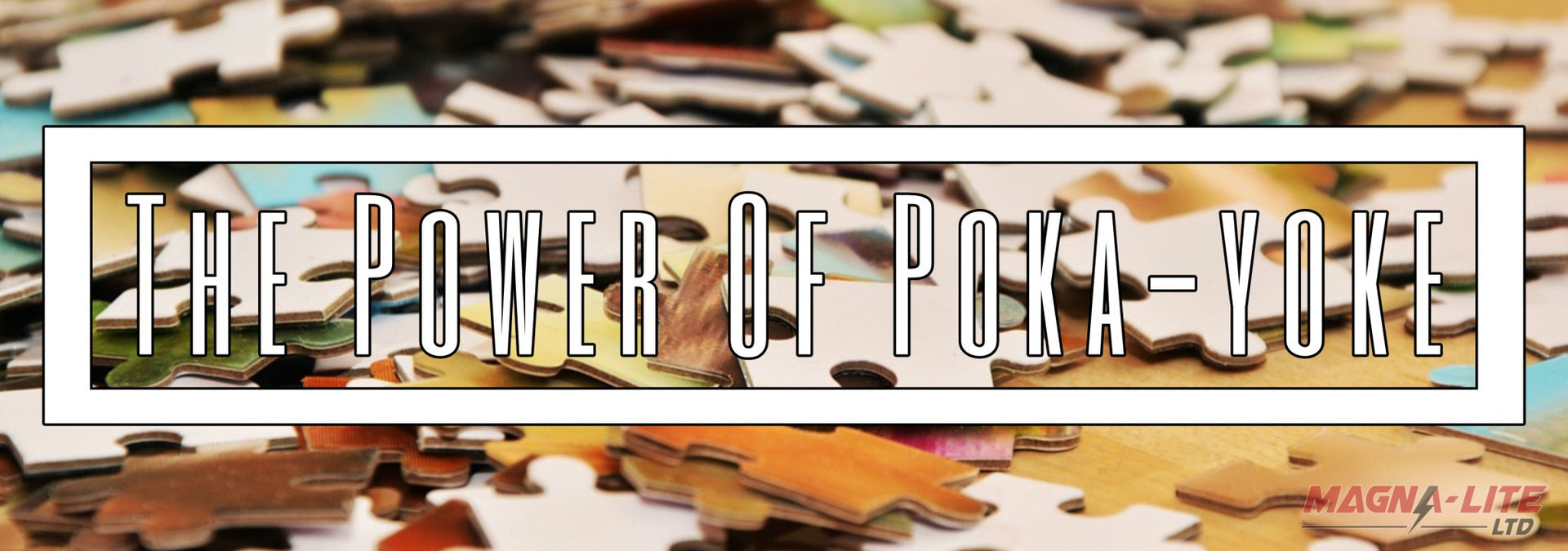
Mastering Mistake-Proofing: The Power of Poka-yoke
In the realm of process optimization and quality assurance, there's a Japanese term that stands out for its profound impact: Poka-yoke (pronounced poh-kuh YOH-kay). Derived from the Japanese words "poka" (mistake) and "yokeru" (to avoid), poka-yoke is a philosophy and methodology aimed at preventing errors before they occur, offering a powerful solution for enhancing efficiency and quality control in various industries. Join us on a journey as we delve into the fascinating world of poka-yoke and explore its significance in modern-day processes.
Originating from Japan, the term "poka-yoke" was coined by Shigeo Shingo, a renowned industrial engineer and key figure in the development of the Toyota Production System (TPS). Shingo introduced the concept in the 1960s as part of his efforts to eliminate errors and defects in their manufacturing processes. With the goal of achieving zero defects, poka-yoke techniques were rooted in the mentality of kaizen, or continuous improvement and became instrumental in fostering a culture of innovation and excellence within their operations. Today, it remains a vital component of lean methodologies, exemplifying the relentless pursuit of perfection and the commitment to continual improvement.
Implementing poka-yoke is advantageous for businesses experiencing frequent defects, high error rates, or struggling to meet quality standards, while industries with stringent regulations, like automotive or pharmaceuticals, can benefit from poka-yoke to ensure compliance. Additionally, organizations aiming to foster a culture of continuous improvement and innovation can leverage poka-yoke as a proactive tool to prevent errors before they even occur. In general, any business prioritizing quality, efficiency, and excellence should consider integrating poka-yoke techniques into its processes.
Implementing Poka-yoke in a business involves a systematic approach to error prevention and continuous improvement. Here are five key steps to help integrate poka-yoke techniques into your operations:
- Identify Potential Errors: Conduct a thorough analysis of your manufacturing processes to identify potential sources of errors or defects. This could involve observing workflows, analyzing historical data, and engaging with frontline workers to gain insights into common issues.
- Design Poka-yoke Solutions: Once potential errors have been identified, work to develop poka-yoke solutions that address these issues proactively. This could include implementing visual cues, physical barriers, or automatic shut-off mechanisms to prevent errors from occurring.
- Test and Refine: Before fully implementing poka-yoke solutions, conduct pilot tests to assess their effectiveness in real-world scenarios. Gather feedback from employees and stakeholders, while making any necessary adjustments to optimize the solutions.
- Train Employees: Provide comprehensive training to employees on the use and maintenance of poka-yoke systems. Ensure that all team members understand the purpose of these solutions and their role in error prevention.
- Monitor and Improve: Continuously monitor the performance of poka-yoke systems and gather feedback from employees to identify any areas for improvement. Regularly review and refine your poka-yoke solutions to ensure they remain effective in preventing errors and promoting quality assurance.
Businesses that have implemented poka-yoke techniques have witnessed significant improvements in quality control, operational efficiency, and cost reduction. For example, a study conducted by the International Journal of Production Economics found that companies achieved a 50% reduction in defects and a 40% decrease in rework costs on average after implementing poka-yoke solutions in their assembly lines. This demonstrates how poka-yoke can drive tangible benefits for businesses, leading to improved product quality, streamlined processes, and enhanced competitiveness in the market. Not to mention the morale boost that employees experience when their suggestions lead to such huge wins for the company!
To summarize, poka-yoke is a pivotal methodology for error prevention and continuous improvement, rooted in the innovative practices of Shigeo Shingo and the Toyota Production System. Businesses that integrate poka-yoke techniques witness tangible benefits, including enhanced quality control, increased efficiency, and reduced costs. For further exploration of poka-yoke and its applications, the book "Mistake-Proofing: Designing Errors Out" by John Grout and James M. Chase has been well regarded as a staple in understanding the ins and outs of poka-yoke. Otherwise, stay tuned to our blog for more insights into lean methodology and articles focused on continuous improvement, empowering you to drive excellence in your organization!