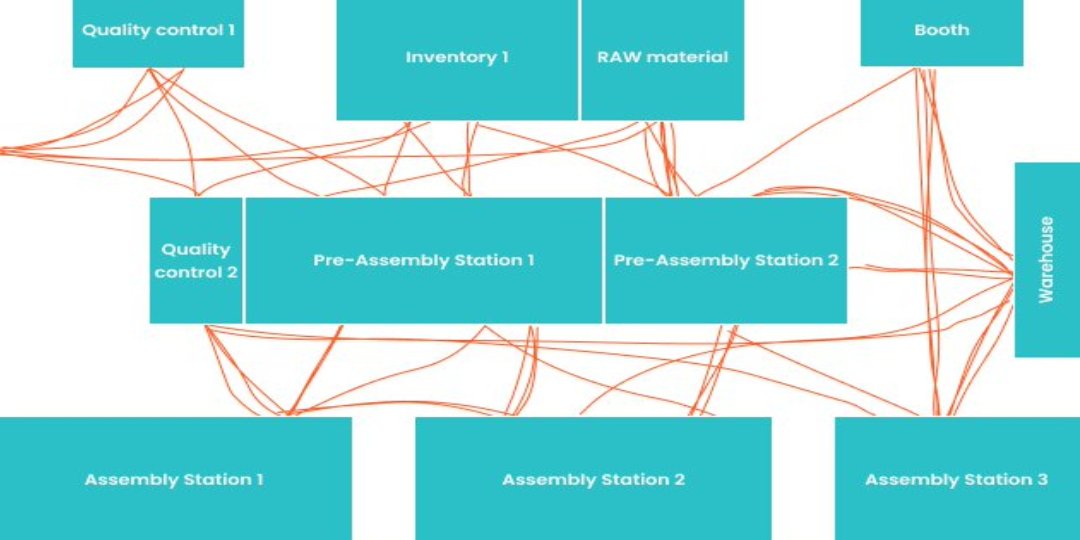
Streamlining Success: Tackling Transportation Waste in Manufacturing
Last month we spoke about the first manufacturing waste of overproduction and how it creates all other wastes along with it. Every manufacturer knows that efficiency is paramount and every inefficiency, no matter how small, can have a ripple effect on productivity and profitability. From unnecessary movement of materials to inefficient layouts, transportation waste can drain resources and hinder progress. In this article, we'll delve into the negative aspects of the second waste of transportation, how to identify it, and simple Lean methods to help improve it.
Identifying Transportation Waste:
Identifying transportation waste requires a keen eye for inefficiencies and a thorough understanding of the manufacturing process. Some common signs of transportation waste include:
-
Excessive Material Handling: Watch for instances where materials are moved multiple times between workstations or storage areas without adding value to the product.
-
Long Travel Distances: Measure the distance traveled by materials or products within the facility. Excessive travel distances indicate potential inefficiencies in layout or workflow.
-
Bottlenecks: Identify areas where materials or products tend to accumulate, causing delays or congestion in the production process.
-
Unnecessary Movement: Look for instances where materials are transported between different production stages when it could be eliminated or minimized through process improvements.
Simple Lean Methods to Improve Transportation Waste:
-
Value Stream Mapping (VSM): Use VSM to visualize the current state of material flow within the manufacturing process. Identify areas of excessive transportation and work collaboratively to design a future state map that eliminates waste and improves efficiency.
-
5S Methodology: Implementing the principles of 5S (Sort, Set in Order, Shine, Standardize, Sustain) can help improve organization and layout within the facility. By organizing work areas and eliminating clutter, you can reduce unnecessary transportation and improve overall efficiency.
-
Just-In-Time (JIT) Inventory: Adopting a JIT inventory system helps minimize excess inventory and reduce the need for transportation and handling of materials. By producing and delivering materials only as needed, you can streamline the flow of materials and reduce waste.
-
Kanban System: Implement a Kanban system to signal when materials need to be replenished or moved within the manufacturing process. This visual management tool helps prevent overproduction and ensures that materials are transported only when necessary.
To summarize, by identifying and addressing transportation waste in manufacturing, organizations can streamline their operations, reduce costs, and improve overall efficiency. Through the implementation of simple Lean methods such as value stream mapping, 5S, JIT inventory, and Kanban systems, companies can optimize material flow and drive sustainable improvement in their manufacturing processes.