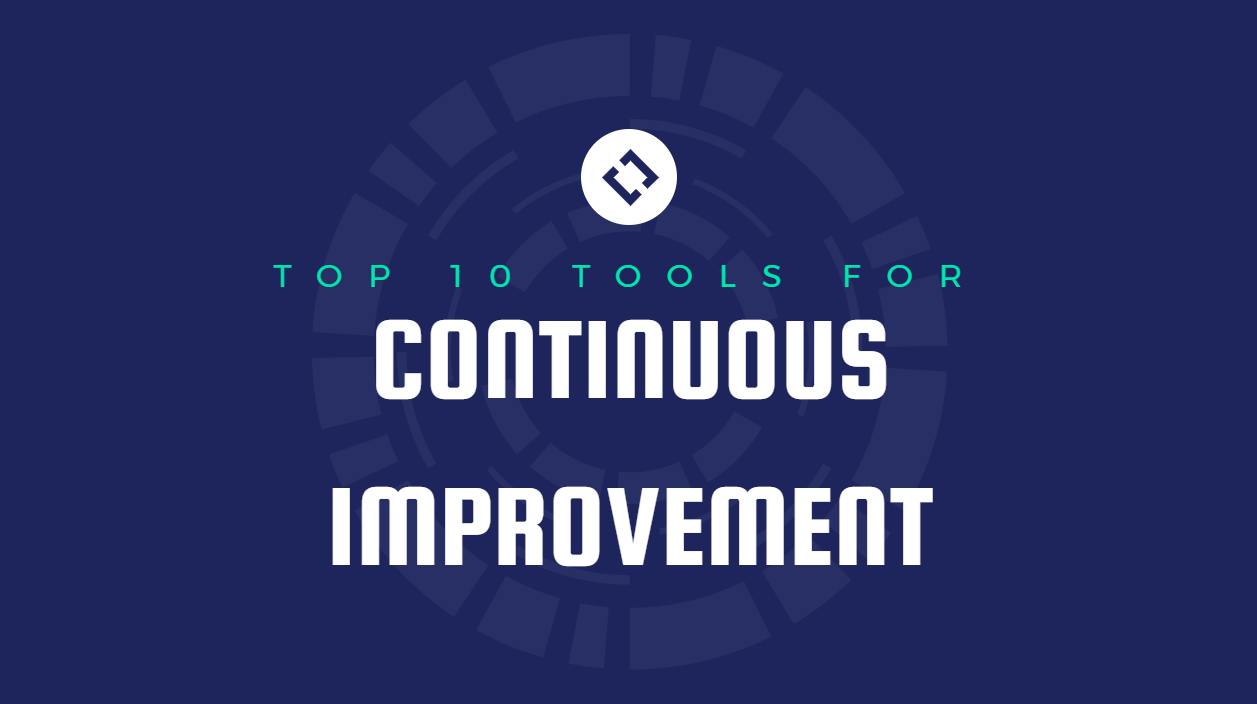
Top 10 Tools for Continuous Improvement
Continuous improvement is a vital aspect of modern business practices, particularly in manufacturing and service industries. Here are the top ten tools that are indispensable in this journey, each with its unique strength and common mistakes that may have them coming up short of your expectations. These are not in order of importance, and just our list of tools we enjoy using at Magna-Lite.
#1 - 2 Second Lean
- Why It's Great: It's all about making small, quick improvements daily. The idea is simple yet powerful: if everyone in an organization saves just 2 seconds per day through minor tweaks, the cumulative effect can be tremendous. It fosters a culture of constant, incremental improvement and engagement.
- Common Mistakes: Overemphasis on minor improvements can lead to neglecting larger systemic issues. There's a risk of trivializing the need for more in-depth changes.
#2 - Cycle Time Reduction
- Why It's Great: This is about efficiency – reducing the time it takes to complete a process from start to finish. By focusing on cycle time, organizations can identify bottlenecks and eliminate waste, leading to faster production times and increased productivity.
- Common Mistakes: Obsessing over speed can sometimes come at the expense of quality, leading to mistakes and poor-quality outputs.
#3 - 5S (Sort, Set in order, Shine, Standardize, Sustain)
- Why It's Great: 5S is fantastic for organizing the workplace. It enhances efficiency and safety, reduces waste, and helps maintain a disciplined work environment. It's not just about cleaning; it's a systematic approach to improving the workplace.
- Common Mistakes: Treating 5S as a one-time event instead of an ongoing process can lead to the gradual return of clutter and disorganization.
#4 - SMED (Single-Minute Exchange of Dies)
- Why It's Great: In industries where equipment setup times are significant, SMED can be a game-changer. By reducing setup times, it drastically increases machine availability and production flexibility.
- Common Mistakes: Hurried setups without adequate planning or training can lead to mistakes, equipment damage, and safety hazards.
#5 - FMEA (Failure Modes and Effects Analysis)
- Why It's Great: This is about proactive problem-solving. FMEA helps in anticipating potential failures in a process and implementing solutions to prevent them. It's a great way to enhance reliability and quality.
- Common Mistakes: Incomplete analysis or infrequent updates can cause some risks to be overlooked, defeating the purpose of the exercise.
#6 - Learning Kata & Coaching Kata
- Why It's Great: These are about building a continuous improvement mindset. The Learning Kata is a pattern of thinking that helps in navigating through unknowns, while the Coaching Kata supports it by fostering a culture of mentoring and continuous learning.
- Common Mistakes: Inconsistent practice and lack of commitment can lead to superficial implementation, failing to instill the intended culture of continuous improvement.
#7 - Fishbone Diagram
- Why It's Great: It's an excellent tool for root cause analysis. By visually mapping out causes and their effects, it helps teams to systematically analyze and address complex problems.
- Common Mistakes: Focusing too much on symptoms rather than root causes can lead to temporary fixes rather than sustainable solutions.
#8 - 5 Whys (Informal Use)
- Why It's Great: It's a simple yet effective tool for root cause analysis. By asking 'why' repeatedly, it helps dig deeper into problems. Its informal use encourages more free-flowing, less structured problem-solving discussions.
- Common Mistakes: Stopping the inquiry too soon can result in superficial solutions that don’t address the root cause. Leading questions can also skew the results and may miss the actual root cause.
#9 - Kanban
- Why It's Great: Kanban enhances workflow visibility and helps manage work-in-progress effectively. It's a fantastic tool for ensuring that production aligns with demand and reducing inventory levels.
- Common Mistakes: Overcomplicating the Kanban system or not adapting it to current processes can lead to inefficiencies and confusion.
#10 - Poka-Yoke (Error Proofing)
- Why It's Great: Poka-Yoke is about preventing errors before they occur. It's a brilliant way to design processes that make it difficult or impossible to make mistakes, thereby improving quality and efficiency.
- Common Mistakes: Excessive reliance on Poka-Yoke can lead to overlooking the need for fundamental training and process improvements.
Each of these tools offers a unique approach to enhancing productivity and efficiency. The key is not just in their implementation but in fostering a culture that embraces continuous improvement as a core value.